What is welding?
Welding is a process that involves joining two or more pieces of metal together using extreme heat and pressure. It is a crucial technique in many industries, including manufacturing, construction, automotive, and aerospace. Welding can be done using various methods, such as stick welding, TIG welding, MIG welding, and flux-cored welding, each with its own advantages and applications. The base metal is melted and fused together with the help of a filler material, creating a strong and durable bond. This versatile technique allows for the fabrication of custom metal structures, repairs to broken or damaged parts, and the creation of intricate and precise designs. Skilled welders, equipped with state-of-the-art welding equipment and expertise, can provide professional welding services with a high level of quality and precision. Whether it’s a residential project, a specialized welding job, or an emergency repair, welding shops near you, Mid Island Steel in Medford New York for example, can offer a wide range of welding services to meet your needs.
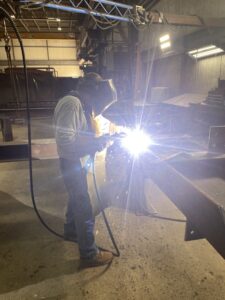
welding shop near me
Benefits of Having Access to a Welding Shop Nearby
Having access to a welding shop nearby offers numerous benefits for individuals and businesses alike. The convenience of having a welding shop nearby means that services are readily available when needed. Whether it’s a quick repair or a complex welding project, having a welding shop in close proximity ensures timely and efficient services.
One of the key advantages of a nearby welding shop is the access to professional expertise. Experienced welders in the shop are skilled in various welding techniques and have a deep understanding of different types of metals and materials. This expertise allows them to handle even the most complex welding projects with precision and accuracy, ensuring high-quality results.
Timeliness is crucial in welding projects, especially when it comes to repairs or urgent modifications. With a nearby welding shop, you can expect prompt and efficient services, minimizing downtime and maximizing productivity. Whether it’s for residential or commercial projects, having easy access to professional welders ensures that your welding needs are met in a timely manner.
In conclusion, having a welding shop nearby offers the convenience of quick and reliable services, the advantage of professional expertise and experience, and the capability to handle complex welding projects. Whether it’s for repairs, modifications, or custom fabrication, accessing a nearby welding shop ensures that your welding needs are met efficiently and effectively.
Types of Welding
When it comes to welding, there are various types of techniques that can be employed depending on the specific requirements of a project. Let’s take a closer look at some of the most common and widely-used types of welding.
1. Stick Welding: Also known as Shielded Metal Arc Welding (SMAW), stick welding is a versatile option commonly used for its portability. It involves the use of an electric current to create an arc between a flux-coated electrode and the base metal, resulting in a strong weld. Stick welding is suitable for a wide variety of materials and is commonly used in construction, fabrication, and repair work.
2. MIG Welding: Short for Metal Inert Gas Welding, MIG welding utilizes a wire electrode that melts and joins the pieces of metal together. This type of welding offers a high level of versatility and is commonly used for automotive repairs, fabrication, and manufacturing. The use of an inert gas, such as argon or helium, shields the weld from contamination and results in clean and strong welds.
3. TIG Welding: Tungsten Inert Gas (TIG) welding is a precise and versatile type of welding that uses a non-consumable tungsten electrode and a separate filler material. TIG welding produces high-quality welds and is often used for projects involving stainless steel, aluminum, and other non-ferrous metals. It is commonly employed in aerospace, automotive, and precision fabrication industries.
4. Flux-Cored Arc Welding: Flux-Cored Arc Welding (FCAW) is similar to MIG welding, but it uses a continuously fed tubular electrode filled with flux. This type of welding is known for its high deposition rates and is often used in construction, shipbuilding, and heavy equipment repair. FCAW can be utilized with or without shielding gas, making it a versatile option for both indoor and outdoor welding projects.
By having a good understanding of these various types of welding techniques, you can select the most suitable method for your specific project needs. Whether it’s stick welding for portability and versatility, MIG welding for clean and efficient results, TIG welding for precision and non-ferrous metals, or flux-cored arc welding for high deposition rates, a nearby welding shop will have the expertise and equipment to handle any welding project with precision and quality.
Stick Welding
Stick welding, also known as Shielded Metal Arc Welding (SMAW), is a widely-used welding technique that offers several benefits for various applications. The process involves creating an arc between a flux-coated electrode (stick) and the base metal. As the electrode melts, it forms a shielded molten pool that solidifies to create a strong weld.
One of the main advantages of stick welding is its portability. This makes it suitable for construction sites and remote locations where access to electricity may be limited. Stick welding can be performed on a wide range of materials, including carbon steel, stainless steel, cast iron, and aluminum.
Another benefit of stick welding is its versatility. It can be used for fabrication, repairs, and structural welding projects. The stick electrode can be easily changed to match the specific requirements of the project, allowing for flexibility and adaptability.
However, stick welding also has its disadvantages. It produces more smoke and fumes compared to other welding processes, making it necessary to have proper ventilation and respiratory protection. Stick welding is also relatively slower compared to some other techniques, which may not be ideal for time-sensitive projects.
In conclusion, stick welding is a valuable welding technique that offers portability, versatility, and the ability to work with a wide range of materials. While it has some drawbacks, its benefits make it a popular choice for welding shops and professionals.
Tig Welding
Tig welding, also known as Tungsten Inert Gas welding, is a complex and high-quality welding technique that produces stronger and cleaner welds. It involves the use of a non-consumable tungsten electrode to create the weld and a shielding gas such as argon to protect the weld area from contamination.
One of the main advantages of Tig welding is its ability to produce strong and precise welds on a variety of materials, including stainless steel, aluminum, and copper. This makes it a popular choice for industries that require high-quality welds, such as aerospace, automotive, and manufacturing.
Tig welding also provides cleaner results compared to other welding processes. The use of a shielding gas eliminates the need for flux, resulting in minimal spatter and a smooth, aesthetically pleasing weld bead. Additionally, Tig welding allows for greater control over the heat input, reducing the risk of distortion or warping of the metal.
Mid Island Steel is known for its expertise in Tig welding. Their team of skilled welders specializes in this technique, ensuring that every weld is of the highest quality. Whether it’s for creating intricate designs or joining critical components, you can trust Mid Island Steel to deliver strong and precise Tig welding services.
In conclusion, Tig welding is a complex and high-quality welding technique that produces stronger and cleaner welds. With Mid Island Steel’s expertise in Tig welding, you can expect exceptional results for your welding projects.
Gas Welding
Gas welding is a widely used technique in commercial and industrial settings due to its versatility and range of applications. This welding process utilizes a combination of fuel gas and oxygen to generate a high-temperature flame, which melts the base metal and filler material to create a strong bond.
In the automotive industry, gas welding is commonly employed for repairs and fabrications of various components. Whether it’s repairing cracked transmission cases or custom-fabricating exhaust systems, gas welding provides the necessary precision and strength to ensure reliable automotive parts.
Gas welding is also ideal for constructing gates and fences. The ability to join metal components together with ease allows for the creation of sturdy and durable structures that can withstand the elements and provide security.
Additionally, gas welding is utilized in pipe welding applications. Whether it’s for industrial or residential plumbing systems, gas welding enables the reliable joining of metal pipes, ensuring leak-free connections and optimal flow.
Furthermore, gas welding is extensively used in metal framing and structural steel construction. Its versatility allows for the fabrication of beams, columns, and trusses, providing the necessary structural support in commercial and residential steel construction projects.
Overall, gas welding offers specialized welding services that cater to various industries and applications. From automotive parts to gates, fences, pipes, and structural steel construction, this technique provides the strength and versatility required in commercial and industrial settings.
Underwater Welding
Underwater welding is a specialized type of welding that takes place in an aquatic environment, typically in a marine or offshore setting. This challenging process is used in various applications and requires exceptional skill and training due to the unique conditions and hazards involved.
The process of underwater welding involves using specialized welding equipment and techniques to join metal components together underwater. Two main techniques used in underwater welding are wet welding and dry welding. Wet welding involves using electrodes that are specifically designed for underwater use, while dry welding is carried out inside a sealed chamber with the water excluded.
Underwater welding finds applications in a range of industries, including marine construction, offshore oil and gas, ship repair, and underwater infrastructure maintenance. It is used to repair and join metal structures such as pipelines, ship hulls, underwater platforms, and offshore drilling equipment.
However, underwater welding presents significant challenges and safety considerations. The welding environment is hostile, with factors such as water pressure, low visibility, and limited access making the task more complex. Divers must have extensive training in both welding and diving techniques to ensure safety and effectiveness. Additionally, precautions must be taken to prevent electric shock and protect against hazardous gases such as hydrogen and carbon monoxide.
In conclusion, underwater welding is a specialized process with unique applications and challenges. Skilled and well-trained divers are essential to carry out this type of welding, and strict safety measures must be followed to mitigate risks and ensure successful underwater welds.
Pipe Welding
Pipe welding plays a crucial role in various industries, serving as an essential method for joining and fabricating pipes of different materials. It finds applications across multiple sectors, including automotive manufacturing, construction, infrastructure development, and plumbing systems.
In the automotive industry, pipe welding is used extensively for creating exhaust systems, fuel lines, and radiator pipes. The precise welding techniques employed contribute to the efficiency and durability of these automotive parts.
Pipe welding also has a significant presence in the construction industry, where it is utilized for fabricating gates, fences, and other structural components. The expertise of professional welders allows them to handle complex projects and ensure the strength and integrity of these structures.
Professional welders specializing in pipe welding possess the necessary skills to repair, modify, and maintain various types of machinery used in industrial settings. They have extensive knowledge of different pipe materials and welding techniques, enabling them to work on diverse projects with precision.
When it comes to pipe welding, it is crucial to rely on experienced professionals who can deliver high-quality results. Their expertise, combined with advanced welding equipment and techniques, ensures the strength, durability, and safety of the welded joints.
In conclusion, pipe welding serves a wide range of industrial applications, including automotive parts, gates, fences, and plumbing systems. Expertise in pipe welding enables professional welders to handle various projects, providing reliable repair, modification, and maintenance services for different types of machinery.
Other Types of Specialized Weldings (i.e. sheet metal welding, stainless steel welding, etc.)
In addition to pipe welding, there are various other types of specialized welding techniques that are commonly used in commercial and industrial applications. Two such techniques include sheet metal welding and stainless steel welding.
Sheet metal welding involves joining two or more pieces of thin metal together using a welding process specifically designed for this type of material. This type of welding is often used in the fabrication of automotive bodies, aircraft panels, and HVAC systems. Sheet metal welding offers several advantages, including improved strength, enhanced aesthetics, and increased resistance to corrosion.
On the other hand, stainless steel welding is a technique used to join stainless steel components. Stainless steel is widely used in industries such as food processing, pharmaceuticals, and chemical manufacturing due to its excellent corrosion resistance and hygiene properties. Stainless steel welds require specialized techniques to maintain the material’s corrosion resistance and to prevent heat distortion. Skilled welders trained in stainless steel welding can produce high-quality, durable welds that meet the stringent requirements of these industries.
Both sheet metal welding and stainless steel welding require specific knowledge, expertise, and equipment to ensure the quality and integrity of the welds. Hiring professional welders experienced in these specialized welding techniques is crucial for achieving reliable and long-lasting results in commercial and industrial applications.
Mobile Services Available for Those in Need of Professional Welder Services
If you are in need of professional welding services but don’t have the time or means to take your project to a traditional welding shop, mobile welding services can be a versatile and convenient option for you. Mobile welding services offer the flexibility of bringing skilled welders and welding equipment directly to your location, whether it’s a residential property or a commercial site. These services are particularly beneficial for clients with custom projects or repairs that require on-site welding expertise. With mobile services, you can have professional welders work on a wide variety of welding projects, from stick welding to TIG welding, and even specialized techniques like underwater welding. The convenience of mobile welding services allows you to take advantage of top-quality welding without the need to transport heavy or bulky metal materials to a welding shop. Whether you need welding repairs, custom metal fabrication, or any other welding service, mobile welding services provide a practical and reliable solution for your welding needs.
Benefits of Mobile Services
Mobile welding services offer numerous benefits to customers who require welding services for various purposes such as boats, vehicles, heavy machinery, industrial, and commercial needs. One of the key advantages is the convenience it offers. With mobile services, customers no longer have to transport their welding projects to a fixed location. The welding shop comes to them, saving time and effort.
Additionally, mobile services provide accessibility to customers. Whether they are located in remote areas or have tight schedules that make it difficult to visit a welding shop, mobile services bridge the gap. This allows customers to access welding services wherever and whenever they need them.
Another benefit is the versatility of mobile services. Welders who offer mobile services have the capability to work on a wide range of welding projects. From custom metal fabrication to repairing boats or vehicles, mobile welders can handle various welding needs with ease.
Lastly, mobile services cater to both industrial and commercial clients. Whether it is welding heavy machinery at an industrial site or repairing commercial structures, mobile welders have the skills and expertise to deliver quality welding services.
In conclusion, mobile welding services bring convenience, accessibility, versatility, and cater to different welding needs of customers, be it for boats, vehicles, heavy machinery, industrial, or commercial purposes.
Range of Mobile Services Offered
Mid Island Steel offers a comprehensive range of mobile services for welding projects. With their expertise and flexibility, they cater to a variety of industries and applications, especially structural steel for both commercial and residential projects.
Mid Island Steel offers only on-site welding services for both residential and commercial clients. From structural steel fabrication to steel supply, our team can handle a wide range of welding needs, ensuring reliable and durable solutions.
Heavy machinery repair requires precision and expertise, and Mid Island Steel’s welders are up to the task. Whether it’s field welding on construction sites or repairing industrial equipment in our welding shop, our professional welders deliver quality workmanship to keep operations running smoothly.
Industrial and commercial projects often involve large-scale welding needs, and Mid Island Steel understands the importance of timely and efficient services. Overall, Mid Island Steel’s range of welding services encompass welding projects for residential steel, commercial steel, heavy machinery, industrial, and commercial applications. We provide clients with reliable and efficient solutions wherever they need them.
Advantages and Challenges with Mobile Services
Mobile welding services offer numerous advantages for customers in Suffolk County and Nassau County, NY. One key benefit is the convenience they provide. With mobile services, professional welders can come directly to the customer’s location, eliminating the need to transport large or heavy items to a welding shop. This saves time and effort on the customers part.
Another advantage is the accessibility of mobile services. They allow customers in remote or hard-to-reach areas to access welding expertise without the hassle of traveling long distances. This is particularly beneficial for those in Suffolk County and Nassau County who may not have easy access to welding shops.
However, mobile welding services also come with their own set of challenges. One challenge is the need for proper equipment and tools that can be transported to the customer’s location. Skilled welders must ensure they have all the necessary welding equipment, such as welding machines and safety gear, to perform the job effectively and safely.
Additionally, mobile welders must be prepared to handle different types of projects and materials. They should be knowledgeable and experienced in working with various metals, such as aluminum, stainless steel, and iron, as well as different welding techniques like MIG, TIG, and stick welding.
Overall, the advantages of convenience and accessibility make mobile welding services a versatile option for customers in Suffolk County and Nassau County, NY.
Quality Control Standards and Procedures For Professional Welder Services
Professional welder services prioritize quality control standards and have rigorous procedures in place to ensure their work meets the highest standards of excellence. This commitment to quality is essential for creating strong and durable welds that can withstand the test of time.
One of the key aspects of quality control is the use of certified welders. Welding certifications are highly valued in the industry as they demonstrate a welder’s competence and skill level. By hiring certified welders, customers can have confidence in the quality of the work being performed.
When searching for professional welder services, it is important to look for certifications from reputable organizations such as the American Welding Society (AWS) and Certified Welders (CW). These certifications provide assurance that the welder has undergone rigorous training and testing to demonstrate their proficiency in various welding techniques and materials.
Quality control also involves implementing strict procedures throughout the welding process. This includes thorough inspections of materials, proper preparation of surfaces, precise measurement and alignment, and careful execution of the welding process itself. Regular quality checks and inspections are conducted to ensure that all welds meet the required standards and specifications.
By adhering to these quality control standards and procedures, professional welder services ensure that their work is of the highest quality, delivering welds that are strong, reliable, and long-lasting.
Benefits From Working With Professional Welder Services
When it comes to welding, quality and precision are paramount. That’s why it’s essential to hire professional welder services. One of the key benefits of working with these experts is their certification. Certified welders have completed extensive training and testing, demonstrating a high level of competence in various welding techniques and materials. This certification ensures that they adhere to industry codes and regulations, guaranteeing quality workmanship.
By hiring certified welders, you can have peace of mind knowing that your project is in capable hands. Their training and experience enable them to tackle complex welding tasks with proficiency and precision. They have a deep understanding of proper procedures, from material inspections and surface preparation to precise measurements and alignment. This ensures that every weld meets the required standards and specifications.
In addition to certification, there are other factors to consider when selecting welding services. It’s important to choose a provider that is fully insured, protecting you from any unforeseen accidents or damages. Look for companies that offer guarantees on their work, demonstrating their confidence in their craftsmanship. It’s also advisable to check their credentials and reviews from previous customers to ensure their track record of delivering quality work.
Investing in professional welder services not only ensures the highest level of competence and quality work, but it also provides you with the peace of mind that your project will be completed to your satisfaction.
Mid Island Steel – Best Welding Shop Near You
Mid Island Steel is the best welding shop near you, offering a wide range of professional welding services. With a team of skilled and certified welders, they have the expertise to handle any welding project with precision and proficiency. From mobile welding services to custom metal fabrication projects, they are equipped to tackle both residential and commercial welding needs. Mid Island Steel takes pride in their level of quality and attention to detail, ensuring that every weld meets the required standards and specifications. With their extensive experience and state-of-the-art welding equipment, they can handle diverse materials such as stainless steel, sheet metal, and more. As a fully insured company, they prioritize customer satisfaction and offer guarantees on their work. Mid Island Steel’s excellent track record and positive customer reviews make them the go-to choice for all your welding needs. Whether you require welding repairs, pipe welding, or specialized welding services, Mid Island Steel is the trusted provider in the area.
Contact Mid Island Steel For A Free Welding Quote
Are you currently looking for a reliable and skilled welding company for your custom welding projects? Look no further than Mid Island Steel. As a reputable welding company, Mid Island Steel has been providing exceptional welding services in [location] and surrounding areas for years.
At Mid Island Steel, we specialize in design, fabrication, packaging, and delivery for a wide range of custom welding projects. Whether you need welding services for residential projects, commercial purposes, or industrial applications, our team of experienced welders is here to help. We take pride in delivering high-quality welding solutions that meet your specific requirements.
When you choose Mid Island Steel for your welding needs, you can expect top-notch craftsmanship, attention to detail, and excellent customer service. Our team has the expertise and the equipment to handle all types of welding projects, from stainless steel and sheet metal welding to pipe welding and more. We understand the importance of precision and durability when it comes to welding, and we strive to surpass our clients’ expectations with every project.
Contact Mid Island Steel today for a free welding quote. Let us demonstrate our expertise and provide you with top-quality welding solutions tailored to your unique needs. Whether you require design assistance, fabrication services, or packaging and delivery for your custom welding projects, we’ve got you covered. Trust Mid Island Steel for all your welding needs and experience the difference of working with a reliable and professional welding company.